Professional press brake punch and die manufacturers think that there are 3 key factors to purchase CNC bending machine mold: cost, using life and efficiency. These three are interrelated. Take one hair and move the whole body. Therefore, the majority of customers should carry out reasonable deployment to optimize the effect.
Development Direction of Bending Die Cutting Technology
How do punch and die techniques develop?
If we want to improve the production efficiency of metal bending machine, we should use high-speed metal forming in punches and dies technology. This can reduce the processing time of the work pieces. But it also needs to compress the auxiliary time, the standby time and downtime. This is also one of the contents WUXI SHEARCHY Technology is studying now.
Press Brake Punch Cooling and Lubrication
In addition, cooling and lubrication is also one of the contents that have to be mentioned. How to choose the right coolant and lubricant is very important. Because their cost accounts for a certain proportion of the total cost. It cannot be ignored. The effect of cooling and lubrication is also related to the overall machining efficiency. Especially, when we meet some difficult to process materials. if these materials processed to a certain extent, the user must conduct proper cooling. When pouring the coolant, the mold may have hot cracks. This will shorten the life of the mold. So in this respect, we need to improve.
On the other hand, the forming technology of press brake die is related to the adjustment of parameters. We think that from the mold itself, the most fundamental is to improve its service life. In addition, manufacturers should also improve the efficiency and quality of processing. If there is a deviation in machining, it will affect the quality of work piece metal forming. So, we must pay attention to control the error during operation!
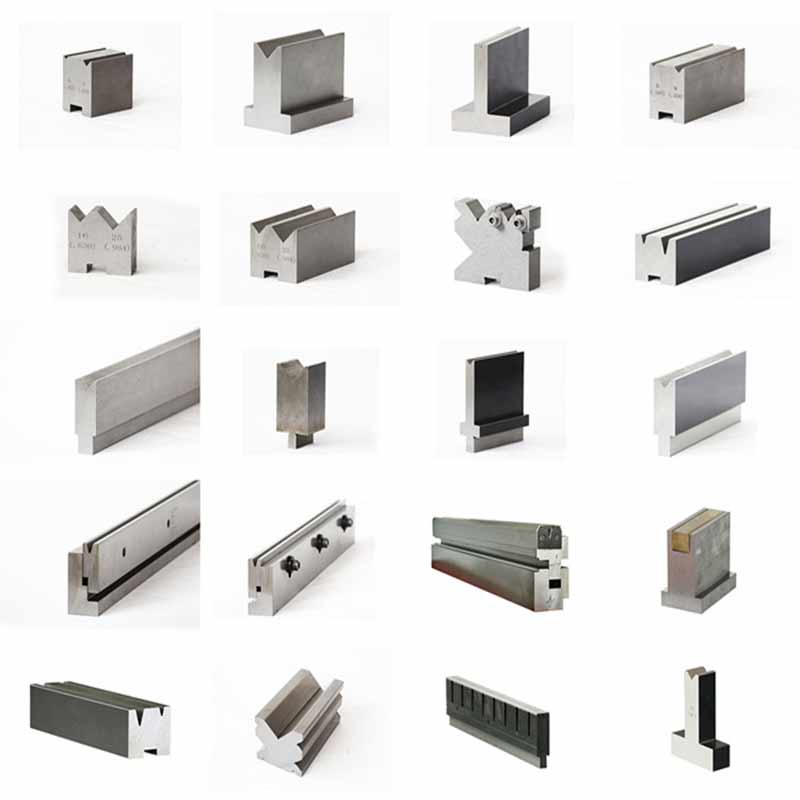
Shearchy Press Brake Punches and Diees Production Process
Down → Forging → Tempering → Finishing → Quenching → Annealing → Conditioning → Coarse Grinding → Finishing → Inspection → Packaging → Factory
Material: 42CrMo, 42CrMo4, SCM440,4140
Holistic heat treatment: Quenching + Tempering + 860 °C Oil quenching + 390°C Tempering
General Hardness: 47+/-2 HRC
Supplying brands: Amada, Tokyo, Komats, Strippit, Trumpf, Finn-power, LVD, Beyeler……
Welcome to contact us with your requirements!